Introduction: Material Reuse and Advanced Sorting
In the quest for a more sustainable future, the cycling industry is increasingly looking towards tech-driven solutions for reducing waste and improving the recycling of materials used in bike production. Recycling has long been a crucial part of any sustainable manufacturing process, and now, advanced technologies such as laser sorting, artificial intelligence (AI), and smart factories are paving the way for a greener future in bike production.
The challenge in cycling manufacturing lies in the fact that many bike components are made from materials that are difficult to recycle or reuse efficiently. Metals like aluminum and steel are common in frames, while tires and plastic parts contribute significantly to waste. Additionally, traditional recycling methods often involve labor-intensive processes that fail to maximize the potential of reusable materials. However, with the advent of innovative sorting techniques and smarter manufacturing processes, tech-driven recycling is poised to transform the way the cycling industry handles its waste.
In this article, we will explore the role of advanced technologies in making bike production more sustainable. From laser-based material sorting to AI-powered systems that streamline recycling, we’ll assess how these innovations can impact the overall environmental footprint of cycling. We’ll also evaluate the costs versus the environmental returns of these tech-driven recycling methods and highlight some of the success stories already making an impact in the industry.
Laser Tech, AI, and Smart Factories
Laser Sorting: The New Frontier in Recycling
One of the most exciting developments in recycling technology is the use of laser-based sorting systems. Traditional methods of sorting materials in recycling plants typically rely on mechanical processes or manual labor, which can be both time-consuming and inefficient. Laser sorting, on the other hand, uses lasers to identify different types of materials based on their optical properties, making it far more accurate and faster than conventional methods.
For instance, laser technology can be used to sort aluminum alloys from steel, plastics, and other materials found in bike frames, parts, and tires. The accuracy of these lasers enables recyclers to capture a higher percentage of usable material for reuse. For the cycling industry, this means less waste, more efficient recycling processes, and potentially cheaper production costs in the long term as more raw materials are recycled back into the supply chain.
Why It Matters:
- Increased Precision: Laser sorting ensures that even the smallest, most complex materials are identified and correctly sorted, leading to higher quality recycled materials.
- Faster Processing: Laser technology significantly reduces the time required to sort materials, allowing manufacturers to recycle more efficiently and scale up operations.
- Cost-Effectiveness: Though initial investments in laser sorting technologies can be high, the long-term savings from increased efficiency and reduced waste can offset these costs.
AI and Smart Factories: Revolutionizing the Recycling Process
Artificial intelligence (AI) is rapidly changing the way we approach manufacturing and recycling. In the context of bike production, AI is being integrated into smart factories, where machines and systems work together to optimize the production and recycling processes. AI can analyze data from sensors embedded in machines, monitor production lines, and even identify defects or inefficiencies in real time. This allows manufacturers to make adjustments to their processes, reducing waste and improving overall sustainability.
Smart factories can incorporate AI algorithms that optimize material usage, predict recycling needs, and determine the most effective ways to process materials. AI-powered systems can also assist in sorting materials, ensuring that only high-quality, recyclable materials are used in production. This level of precision ensures that resources are not wasted, making the production process more sustainable.
Why It Matters:
- Data-Driven Insights: AI helps manufacturers identify trends, patterns, and inefficiencies that can reduce material waste, leading to more sustainable production practices.
- Automated Sorting: AI-powered sorting systems can intelligently categorize materials with little to no human intervention, enhancing the efficiency of recycling processes.
- Predictive Maintenance: AI can predict when machines or equipment need maintenance, reducing the risk of breakdowns that could lead to excess waste or operational inefficiencies.
Smart Factories and Circular Manufacturing
Circular manufacturing focuses on creating a closed-loop production process where products are designed for longevity, easy repair, and eventual recycling. Smart factories are integral to this process because they enable real-time tracking and monitoring of materials as they pass through the various stages of production and recycling. The integration of AI, IoT (Internet of Things), and machine learning into these factories ensures that every part of the manufacturing process is as efficient and sustainable as possible.
Smart factories also promote a “circular economy” by reducing reliance on new raw materials. Through real-time tracking, manufacturers can measure the environmental impact of each component, optimize the use of recycled materials, and create products with minimal waste. For example, bike frames can be produced using recycled aluminum, and plastic components can be made from reclaimed plastics—both processes benefiting from the insights and capabilities of smart factory technology.
Why It Matters:
- Real-Time Efficiency: Smart factories optimize workflows, reduce waste, and improve the recycling process, contributing to a more sustainable manufacturing cycle.
- Closed-Loop Systems: By recycling materials within the same production cycle, manufacturers reduce the need for new resources, which helps protect the environment and conserve raw materials.
- Sustainability Tracking: Smart factories track environmental data such as carbon emissions, energy consumption, and material usage, enabling manufacturers to identify areas for improvement in sustainability.
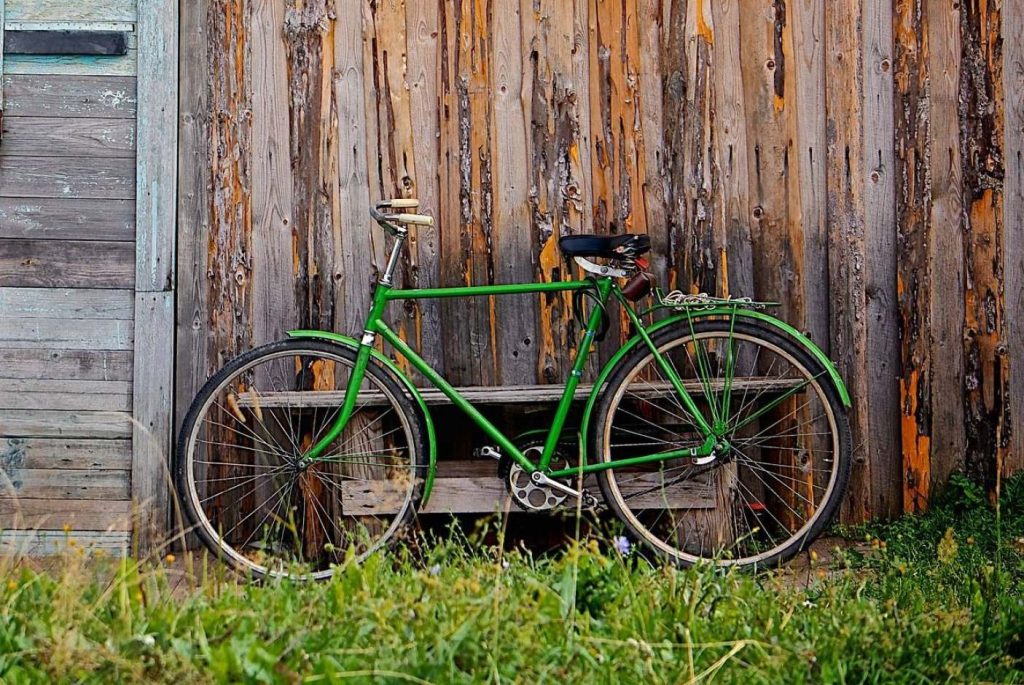
Cost vs. Environmental Return
Initial Investment vs. Long-Term Gains
Tech-driven recycling methods, especially those involving advanced sorting and AI integration, often require significant upfront investment. Laser sorting systems, AI-powered machines, and smart factory infrastructure can be expensive to implement, and not every manufacturer may have the capital to invest in these technologies at the outset. This can create a dilemma: how to balance the high costs of adopting such advanced systems with the environmental benefits they promise.
However, there are several ways in which the long-term environmental return outweighs the initial investment. First, recycling and reusing materials reduce the need for virgin materials, which are often more energy-intensive to produce and come with higher environmental costs. Second, tech-driven recycling systems improve efficiency, leading to less material waste and a more streamlined production process. This results in lower operational costs over time, offsetting the initial investments.
Why It Matters:
- Cost Savings Over Time: While initial investments are high, the long-term savings in reduced waste, lower production costs, and less reliance on raw materials can provide significant returns.
- Environmental Impact: The reduction in waste and energy use, as well as the increased recycling rates, contribute to a significantly smaller environmental footprint for cycling manufacturers.
- Scalability: Once implemented, these systems can be scaled to other production facilities or used across multiple manufacturing stages, maximizing the return on investment.
Balancing Profit and Planet
Tech-driven recycling must be approached with a balance between profit and environmental impact. For some manufacturers, especially smaller ones, the challenge lies in making the business case for implementing such technologies. However, as consumer demand for sustainable products grows, many cycling brands are recognizing that investing in eco-friendly manufacturing processes is not just good for the planet—it’s good for business as well.
Consumers are increasingly interested in purchasing bikes and components that have been produced with sustainability in mind. Eco-conscious shoppers are willing to pay a premium for products that have minimal environmental impact, and this trend is only expected to increase in the coming years. For manufacturers, this shift in consumer behavior presents an opportunity to not only reduce waste but also attract a loyal customer base.
Why It Matters:
- Consumer Demand: Eco-conscious consumers are increasingly seeking out brands that prioritize sustainability, creating a market incentive for manufacturers to adopt tech-driven recycling methods.
- Profitability and Reputation: Manufacturers that embrace sustainable practices can enhance their brand reputation, attract new customers, and potentially increase sales while reducing environmental harm.
Success Cases in the Industry
Several cycling brands have already begun to implement tech-driven recycling solutions, offering a glimpse into the future of the industry. For example, one notable case is a European bicycle manufacturer that has incorporated laser sorting technology to recycle aluminum alloys from old bike frames. The company also uses AI-powered systems to track the performance of recycled materials, ensuring that they meet the same standards as virgin materials. As a result, they have significantly reduced the amount of material waste in their production process and increased the proportion of recycled material used in their bikes.
Another example comes from a major tire manufacturer that has developed a method for recycling old tires into new rubber compounds. Using a combination of AI and smart factory systems, they have been able to create a closed-loop production process that uses tire waste as raw material for new tires, eliminating the need for virgin rubber.
Why It Matters:
- Practical Application: These success stories demonstrate that tech-driven recycling is not just a theoretical concept but a practical solution that is already being implemented in the cycling industry.
- Setting Industry Standards: As these companies lead the way, others will likely follow, creating a ripple effect that encourages wider adoption of tech-driven recycling methods.
Conclusion: Can Tech Solve the Waste Crisis?
Tech-driven recycling holds immense potential for transforming bike production into a more sustainable and eco-friendly process. Laser sorting, AI, and smart factory technologies are all paving the way for more efficient recycling, reducing waste and minimizing the use of virgin materials. While there are significant upfront costs involved, the long-term environmental and financial benefits are undeniable.
As the cycling industry continues to grow, embracing these technologies will be key to addressing the waste crisis and ensuring a greener future for the sport. Manufacturers that invest in advanced recycling methods now will not only reduce their environmental impact but also position themselves as leaders in the sustainable production of cycling products.
With consumer demand for sustainable products on the rise, the industry’s shift toward tech-driven recycling could be the catalyst for a new era of greener bike production. The question is not whether this technology will work, but how quickly the rest of the industry will embrace it.
Discussion about this post