Introduction: What 3D Printing Offers Cycling
The rise of 3D printing, also known as additive manufacturing, has taken industries across the globe by storm, and cycling is no exception. Traditionally, bike frames have been made from materials like aluminum, steel, carbon fiber, and titanium, often using complex processes like welding, molding, and machining. However, 3D printing offers a revolutionary alternative that has the potential to change the way bicycles are designed, produced, and customized.
At its core, 3D printing is a process where material is deposited layer by layer to build a 3D object based on a digital design. This technology has already found significant applications in industries like aerospace, automotive, and healthcare, but its entry into the cycling world represents a new frontier. 3D-printed bike frames promise to unlock a new level of precision, customization, and performance, all while reducing material waste and production time. Early prototypes and production models have already demonstrated the advantages of this technology, but as experts begin to examine its full potential, it raises several questions about its viability, durability, cost, and long-term impact on the cycling industry.
Structural Benefits vs. Cost: Expert Breakdown
One of the primary advantages of 3D-printed bike frames is the ability to produce highly intricate and optimized structures that would be difficult or impossible to achieve with traditional manufacturing methods. With 3D printing, engineers can design bike frames with complex internal geometries, reducing material weight without sacrificing strength. This process, known as “topology optimization,” allows for the creation of lightweight frames with a high strength-to-weight ratio, which is particularly important for high-performance bikes like road, mountain, and racing bicycles.
Experts in the field are particularly excited about the potential of 3D printing to create custom-designed frames that are optimized for specific riders. By using data from motion analysis, biomechanical scans, or rider preferences, 3D printing can produce a frame that perfectly matches the rider’s body geometry and riding style. This level of personalization is almost impossible to achieve with traditional manufacturing, which typically relies on stock frame sizes and standard molds.
However, there are trade-offs. The most significant barrier to widespread adoption of 3D-printed bike frames is cost. Currently, the materials and equipment required for 3D printing are expensive. The process itself can also be time-consuming, as each frame must be printed layer by layer, which contrasts with the speed of mass production techniques. While companies like Specialized and Trek have experimented with 3D-printed components, including seat posts, handlebars, and forks, the production of an entire frame using 3D printing remains a costly endeavor. As a result, it is unlikely that 3D-printed frames will be able to compete with mass-produced aluminum or carbon fiber frames in terms of affordability for the average consumer in the near future.
“3D printing provides an exciting avenue for innovation, but the costs associated with both the materials and the printing process will likely limit its use to high-end, custom-built bikes for elite athletes and enthusiasts in the short term,” says Dr. Lisa Moreau, a materials scientist specializing in advanced manufacturing technologies.
Customization and Ergonomics Potential
One of the most compelling aspects of 3D-printed bike frames is the ability to fully customize the design for individual riders. Unlike traditional methods, where frame sizes and geometries are limited by molds and production processes, 3D printing enables a virtually infinite range of customization options. Riders can now have frames that are tailored to their specific body measurements, riding posture, and performance needs, leading to improved comfort and efficiency.
For example, professional cyclists often struggle with fitting their bikes to their precise body geometry, as even the smallest misalignment can lead to discomfort or decreased performance. With 3D printing, custom frames can be designed to address specific ergonomic issues such as knee angles, back curvature, or hand positioning. This could be a game-changer for athletes and recreational cyclists alike who are looking for a more personalized fit.
Additionally, 3D printing allows for the integration of unique features into the frame design. This could include provisions for mounting additional accessories like custom racks, water bottle cages, or lights, all tailored to the rider’s needs. The ability to design these elements seamlessly into the frame itself rather than as add-ons could improve both aesthetics and functionality.
Beyond professional athletes, recreational cyclists also stand to benefit from custom designs. Many riders struggle to find a frame that fits properly, particularly those with unique body types or specific needs (e.g., taller or shorter riders, those with joint issues). 3D printing could make cycling more accessible by offering solutions to these individuals, leading to a more inclusive cycling experience for all.
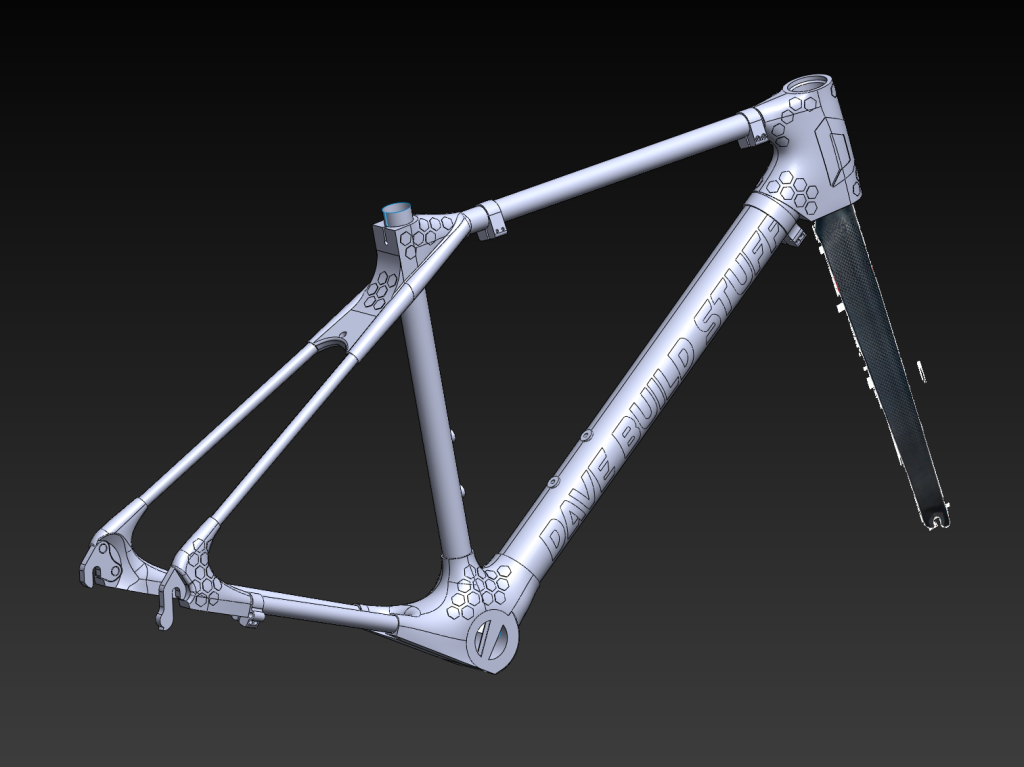
Limitations and Sustainability Angle
While the potential benefits of 3D printing in cycling are exciting, there are several limitations and challenges that need to be addressed. One of the primary concerns is the material selection. Traditional bike frames are made from strong, lightweight materials like carbon fiber and titanium, both of which offer excellent strength-to-weight ratios. While there are 3D-printable alternatives such as carbon fiber-infused filaments, they are not yet as robust or reliable as their traditionally manufactured counterparts. For instance, 3D-printed carbon fiber frames have yet to demonstrate the same level of durability, especially under high-stress conditions like those encountered during mountain biking or long-distance racing.
The technology is also limited in terms of the types of materials that can be used for 3D printing. While metal 3D printing is advancing rapidly, it is still a relatively expensive process that requires specialized equipment. As a result, many 3D-printed bike frames are currently limited to plastic and composite materials, which may not offer the same level of performance as traditional metals like aluminum or titanium.
In terms of sustainability, 3D printing does have some advantages. Traditional manufacturing processes often result in significant material waste, particularly when cutting or molding frames. 3D printing, on the other hand, is an additive process, meaning material is only used where it’s needed, leading to less waste. This makes 3D printing a more environmentally friendly option, especially when paired with sustainable materials. Moreover, because 3D printing allows for rapid prototyping, manufacturers can experiment with new designs and materials without the need for costly and wasteful trial runs.
However, the environmental impact of 3D printing depends largely on the materials used. Some 3D printing filaments, such as certain plastics, are not biodegradable and could pose long-term environmental challenges. The energy consumption associated with 3D printing can also be a concern, particularly when using high-powered printers for metal or composite materials. As the technology evolves, it is likely that more sustainable materials and energy-efficient printing methods will be developed, but this is still a work in progress.
Conclusion: Are We Ready for a 3D-Printed Future?
As the technology surrounding 3D-printed bike frames continues to evolve, experts agree that we are still in the early stages of what could eventually become a major shift in the cycling industry. While there are clear advantages in terms of customization, structural optimization, and reduced material waste, the high cost, limited material selection, and durability concerns present significant obstacles to widespread adoption. Currently, 3D-printed frames are likely to remain a niche offering, primarily for high-end, custom-built bikes aimed at professional athletes or discerning enthusiasts.
The future of 3D-printed bike frames will depend on several factors: advancements in 3D printing technology, improvements in material science, and the ability to scale production in a cost-effective manner. As manufacturers continue to experiment with this technology, the potential for more affordable and widely accessible 3D-printed bikes will likely emerge, but it will take time. For now, the technology promises a tantalizing glimpse into the future of cycling, where personalized, lightweight, and environmentally friendly frames could become the norm—if not tomorrow, then in the years to come.
Discussion about this post