The world of bike manufacturing has been historically dominated by traditional production methods involving casting, forging, welding, and assembling parts made from aluminum, carbon fiber, steel, or titanium. However, the rise of additive manufacturing—more commonly known as 3D printing—has introduced a revolutionary shift in how bicycles can be designed, customized, and produced. Once regarded as a niche technology for prototyping, 3D printing has grown rapidly, showing promise for transforming the cycling industry. From bespoke bike frames tailored to individual riders to rapid prototyping of parts and even fully printed components, the potential of 3D printing in this space is becoming too significant to ignore. This article explores how additive manufacturing is reshaping bike production, evaluates its scalability, and assesses its customization capabilities, all while considering what this could mean for the future of cycling.
Understanding Additive Manufacturing in the Bike Industry
Additive manufacturing, or 3D printing, involves building objects layer by layer from a digital file. This contrasts with subtractive manufacturing, which involves cutting away material from a solid block to form a part. The benefits of additive manufacturing are particularly well-suited to the cycling world: weight savings, design freedom, material efficiency, and the ability to produce highly customized parts without extensive tooling.
There are several 3D printing technologies relevant to the cycling industry, including:
- Selective Laser Melting (SLM) and Direct Metal Laser Sintering (DMLS), which are commonly used for printing strong, load-bearing parts like bike lugs or frame joints from titanium or aluminum.
- Fused Deposition Modeling (FDM), used for quick prototyping or less structural components using polymers.
- Stereolithography (SLA), employed for intricate components, molds, or testing prototypes.
- Carbon DLS (Digital Light Synthesis), used in high-performance components like saddles or shoe soles due to its excellent mechanical properties and high resolution.
This technological landscape offers manufacturers, both large and small, a wide array of options to rethink how bikes and bike parts are made.
Customization Potential: Made-to-Measure Bikes
One of the most compelling aspects of 3D printing in the cycling world is its potential for mass customization. Traditional manufacturing processes are limited by the constraints of molds, tooling, and standardized sizes. In contrast, 3D printing allows for the creation of parts specifically tailored to an individual’s body geometry, riding style, and performance needs.
Several pioneering companies are already offering custom 3D-printed components:
- Bastion Cycles in Australia creates high-end custom bikes with 3D-printed titanium lugs paired with carbon fiber tubes. Each bike is tailored to the customer’s fit and performance specifications.
- Arevo, a California-based company, uses robotic 3D printing and AI-generated designs to produce fully carbon fiber bike frames, optimized for strength and weight.
- Selle Italia and Specialized have introduced 3D-printed saddles with customized padding zones, based on pressure mapping of a rider’s sit bones.
With body scanning and fit analysis becoming more accessible, riders can have bikes built exactly to their measurements. This not only improves comfort and performance but also significantly reduces the chances of injury caused by ill-fitting geometry.
Prototyping and Product Innovation
3D printing is also revolutionizing the speed and efficiency of product development. Traditionally, designing a new component involved lengthy processes: drafting, machining, testing, and repeating. With 3D printing, manufacturers can iterate faster—often within a single day.
For instance, if a design team wants to test a new geometry for a handlebar or dropout, they can print a prototype overnight and begin testing it the next day. This rapid prototyping accelerates innovation cycles and allows companies to experiment with bolder, more experimental designs.
In addition, because digital files are easily modifiable and transportable, design teams across the globe can collaborate in real time. A designer in Berlin can adjust a model and send it to a facility in Taiwan, where the part is printed and evaluated in less than 24 hours.
Lightweight Strength and Complex Geometries
One of the biggest advantages of additive manufacturing is the ability to produce complex geometries that would be difficult or impossible to achieve with traditional methods. Internal lattices, organic shapes, and topology-optimized structures allow parts to be extremely lightweight without compromising strength.
Titanium, in particular, has become a favored material in 3D-printed cycling components due to its high strength-to-weight ratio, corrosion resistance, and fatigue strength. With 3D printing, manufacturers can create hollow lugs with internal reinforcements, brake levers with lattice cores, or pedals with integrated shock absorption.
These geometries also help in improving aerodynamics—a crucial factor in professional racing. By smoothing transitions, optimizing tube shapes, and integrating parts, 3D-printed bikes can achieve better wind resistance performance, offering competitive advantages for elite cyclists.
Sustainability and Localized Manufacturing
Additive manufacturing has notable environmental and logistical benefits. Unlike traditional manufacturing, which often results in significant material waste, 3D printing uses only the material necessary to build the part. This reduces resource consumption and energy use.
Moreover, 3D printing allows for decentralized manufacturing. Instead of producing bikes or components in massive overseas factories and shipping them globally, companies can set up local print farms closer to their customers. This model reduces transportation emissions, lowers inventory costs, and enables quicker turnaround for repairs or replacements.
Several companies are exploring local production hubs where custom frames, saddles, or even wheels are printed on demand, cutting down on global logistics and making cycling products more environmentally friendly.
Scalability: Can 3D Printing Keep Up With Demand?
While the benefits of 3D printing are clear, questions remain about scalability. Traditional manufacturing methods are efficient at mass production once tooling is in place. Can 3D printing compete on volume, cost, and consistency?
The answer depends largely on the application. For mass-market, entry-level bikes, 3D printing is currently not competitive in terms of cost or production speed. However, for mid-to-high-end components and frames, the economics are shifting.
New multi-laser systems and robotic printing farms are increasing production rates significantly. Companies like HP and GE Additive are investing heavily in industrial 3D printing systems capable of producing thousands of parts per week with high consistency. As these technologies continue to mature, the cost per part is expected to drop, making them viable even for broader markets.
Moreover, hybrid manufacturing approaches are gaining popularity. For instance, a bike frame may have 3D-printed joints but use traditional carbon fiber tubes. This combination enables customization where it’s most beneficial while maintaining production efficiency.
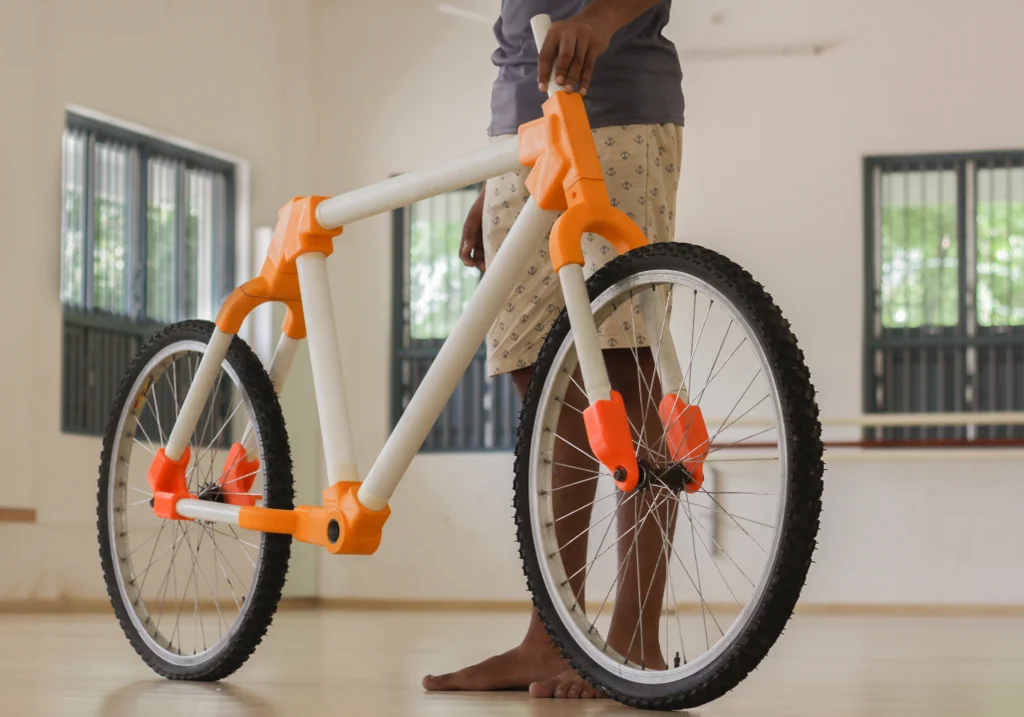
Challenges and Barriers to Adoption
Despite the promise, there are still several hurdles to widespread adoption of 3D printing in bike manufacturing:
- High initial investment in industrial-grade printers and metal powders.
- Material limitations, especially for polymers not yet optimized for long-term outdoor durability.
- Regulatory and safety testing requirements, particularly for load-bearing parts in high-stress areas like forks or handlebars.
- Skilled labor needed to operate, maintain, and optimize advanced printing systems.
There is also a psychological barrier for some consumers. Bikes are deeply personal machines, and the idea of a frame being printed rather than welded or molded may not immediately inspire confidence, especially among traditionalists. Brands will need to build trust through transparency, testing data, and real-world performance validation.
The Future Outlook
The trajectory of 3D printing in bike manufacturing looks optimistic. As materials improve, costs decrease, and production scales up, additive manufacturing is likely to take on a more central role in the cycling industry. Customization will be the key driver—consumers increasingly want products that reflect their individual needs and styles, and 3D printing is uniquely positioned to deliver that.
We may also see a rise in “modular manufacturing,” where standardized components (like bottom brackets or wheel dropouts) are paired with 3D-printed customized elements (like geometry-specific lugs). This blend of scalability and personalization could become the dominant production model for premium and performance-oriented bikes.
More excitingly, the intersection of 3D printing with other technologies—such as AI-driven design, smart materials, and even embedded sensors—could lead to bikes that are not only custom-made but also “smart,” responsive, and self-diagnosing.
Expert Insights
To further understand the implications of this shift, we consulted industry leaders in cycling technology and design.
Eva Lange, Head of Innovation at a European bike brand, notes: “3D printing is allowing us to rethink what a bike can be. We’re no longer restricted by tooling or legacy designs. The possibilities are endless, and we’re only just scratching the surface.”
Dr. Matteo Ricci, a mechanical engineer specializing in additive manufacturing, adds: “The ability to fine-tune strength and weight with topology optimization and print it directly into a bike component is revolutionary. We can tailor stress distribution, airflow, and even vibration damping with digital precision.”
James Lin, a custom frame builder, reflects: “3D printing doesn’t replace craftsmanship—it enhances it. I can offer my customers something completely unique, made for their body and their riding style. That’s powerful.”
Conclusion
3D printing is more than just a futuristic concept—it’s a practical, evolving tool that’s already transforming bike manufacturing. From creating bespoke, performance-optimized frames to enabling rapid prototyping and sustainable production, additive manufacturing offers a glimpse into the next era of cycling innovation. While challenges in cost and scalability remain, the rapid pace of technological advancement suggests these barriers will continue to fall. As the industry embraces a more customized, decentralized, and sustainable model of production, 3D printing stands at the forefront of that change. For cyclists and manufacturers alike, the future is being printed—layer by layer.
Discussion about this post