The Rise of Additive Manufacturing in Bicycle Production
In recent years, the bicycle industry has witnessed a significant transformation with the advent of additive manufacturing, commonly known as 3D printing. This technology has introduced a new paradigm in bike production, enabling manufacturers to create complex geometries, reduce material waste, and accelerate the prototyping process. The integration of 3D printing into bicycle manufacturing is not merely a trend but a substantial shift that promises to redefine the industry’s future.
Advantages of 3D Printing in Bike Manufacturing
One of the most compelling benefits of 3D printing in bike production is the ability to fabricate intricate designs that were previously unattainable through traditional methods. This design freedom allows for the creation of lightweight structures without compromising strength and durability. For instance, manufacturers can produce lattice structures within bike frames, optimizing weight distribution and enhancing performance.
Moreover, 3D printing facilitates rapid prototyping, enabling designers to iterate quickly and efficiently. This agility in the design process accelerates the development of new models and allows for swift adjustments based on testing and feedback. Additionally, the technology supports on-demand production, reducing the need for large inventories and minimizing storage costs.
Customization and Personalization
The demand for customized bicycles has grown substantially, with consumers seeking products tailored to their specific needs and preferences. 3D printing addresses this demand by allowing for the production of bespoke components and frames. Cyclists can now have bikes that fit their exact body measurements, riding styles, and aesthetic preferences. This level of personalization enhances comfort, performance, and overall satisfaction.
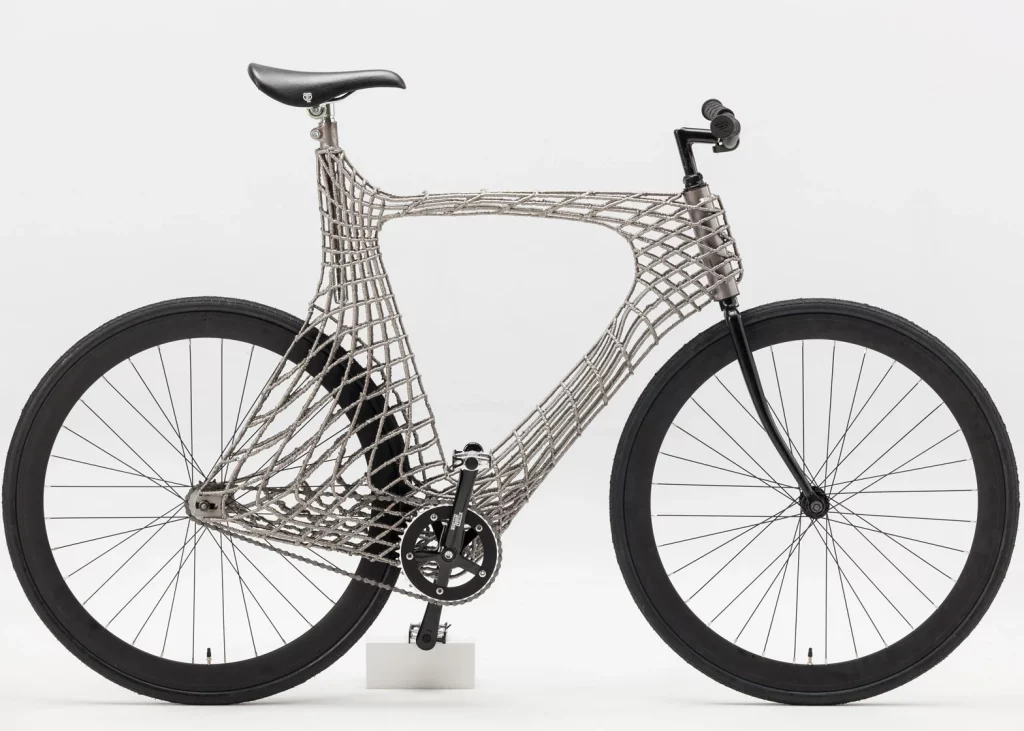
Case Studies: Industry Adoption
Several companies have embraced 3D printing to revolutionize their manufacturing processes. For example, Hanglun Technology utilizes metal 3D printing to produce titanium bike frames that are lighter and more aerodynamic, offering increased speed and reduced turbulence during long-distance rides. Similarly, Urwahn Engineering employs additive manufacturing to create steel frames with unique geometries, combining organic design with high functionality.
Another notable example is Heavy Bikes, which uses 3D printed molds for casting single-piece aluminum frames. This approach streamlines the production process and allows for greater design flexibility, resulting in high-performance bicycles tailored to individual customer requirements.
Challenges and Considerations
Despite its advantages, the integration of 3D printing into bike manufacturing presents certain challenges. The initial investment in 3D printing equipment and technology can be substantial, potentially limiting accessibility for smaller manufacturers. Additionally, the scalability of 3D printing for mass production remains a topic of discussion, as traditional manufacturing methods may still be more cost-effective for large-scale operations.
Material limitations also pose considerations, as not all materials used in traditional bike manufacturing are compatible with 3D printing processes. Ensuring the structural integrity and longevity of 3D printed components requires rigorous testing and quality assurance.
Future Outlook
The trajectory of 3D printing in the bicycle industry suggests a continued expansion and integration of this technology. As advancements in materials and printing techniques evolve, the cost barriers are expected to decrease, making 3D printing more accessible to a broader range of manufacturers. The emphasis on sustainability and efficiency further supports the adoption of additive manufacturing, as it aligns with environmental goals by reducing waste and energy consumption.
In conclusion, 3D printing holds the potential to disrupt traditional bike manufacturing by offering unparalleled design flexibility, customization, and efficiency. While challenges exist, the ongoing developments in this field indicate a promising future where additive manufacturing becomes a cornerstone of bicycle production.
Discussion about this post