Introduction: Industry-Wide Waste Issues
As the world becomes increasingly aware of environmental concerns, manufacturers across industries are grappling with the urgent need to reduce waste and adopt sustainable practices. One area of particular focus is zero-waste manufacturing, where the aim is to eliminate waste in every step of the production process. In industries ranging from fashion to automotive to electronics, companies are scrutinizing their supply chains, design processes, and waste management strategies to minimize their environmental footprints.
The traditional “take-make-dispose” model of manufacturing has long been the dominant paradigm, resulting in significant waste—whether it’s raw materials left unused, defective products discarded, or manufacturing by-products that end up in landfills. However, the growing push for zero-waste manufacturing aims to turn this cycle on its head by ensuring that the value in every material and resource is maximized. This push is not just driven by environmental concerns but also by market demand for more responsible, sustainable business practices, government regulations, and a commitment to a circular economy.
The growing adoption of zero-waste practices reflects a broader trend of sustainability in manufacturing, and it’s gaining momentum across industries. From large multinational corporations to small startups, a collective shift is occurring as companies begin to see both environmental benefits and long-term economic advantages from reducing waste.
Process Innovations: Molding, Welding, Materials
A significant aspect of achieving zero-waste manufacturing lies in process innovations. Manufacturers are finding new ways to create products with minimal waste, incorporating advanced technologies and materials to make production cleaner, more efficient, and more sustainable.
1. Molding and Forming Techniques
One of the most common sources of waste in manufacturing is the process of shaping raw materials into components, such as through molding or casting. These techniques often result in excess material that can’t be reused, leading to significant amounts of scrap. Innovations in molding and forming techniques have been key in minimizing waste.
For example, precision molding, which uses high-accuracy machines to form materials into precise shapes, reduces excess material and ensures that more of the raw input is converted into usable products. Companies are also exploring additive manufacturing (3D printing) as a way to reduce waste, as it allows for the precise construction of products layer by layer. This process not only reduces material wastage but also cuts down on energy consumption and production time.
In some industries, companies are exploring “near-net-shape” techniques, which aim to create components that are already close to their final form, minimizing the need for further machining or processing. This reduces the amount of material lost during manufacturing.
2. Welding and Joining Innovations
Welding is another manufacturing process that can lead to significant waste due to spatter, excess heat, and the production of scrap. Innovations in welding technology, such as laser welding and friction stir welding, offer more precise and efficient methods, resulting in cleaner, waste-reduced operations.
Laser welding, for example, uses high-powered lasers to melt materials together, reducing the amount of heat and material loss compared to traditional welding techniques. It also leads to better product quality with minimal distortion, reducing the need for post-weld cleaning or repairs, which traditionally contributes to additional waste.
Friction stir welding (FSW), which involves the use of a rotating tool to join materials, is another advancement that generates less waste and requires no filler materials, reducing the production of scrap. This welding technique is becoming particularly popular in industries such as aerospace and automotive, where precision is crucial, and waste reduction is a key sustainability goal.
3. Material Innovation
Material selection plays a crucial role in zero-waste manufacturing. In the past, many industries relied on materials that could not be recycled or were difficult to process. However, the push for zero-waste manufacturing has led to the development of new, sustainable materials that can be reused or repurposed at the end of their lifecycle.
One such example is the use of biodegradable polymers and bioplastics, which are increasingly being integrated into packaging and product designs to reduce plastic waste. These materials are not only more sustainable but are also designed to fit into a circular economy model, where products can be broken down and reused rather than ending up in landfills.
Recycled materials are also playing a significant role in zero-waste initiatives. In sectors like construction and automotive manufacturing, the use of recycled metals, plastics, and textiles is being increasingly incorporated into production. For example, some companies are using recycled aluminum to create lightweight car parts, reducing the need for raw material extraction and lowering the carbon footprint associated with production.
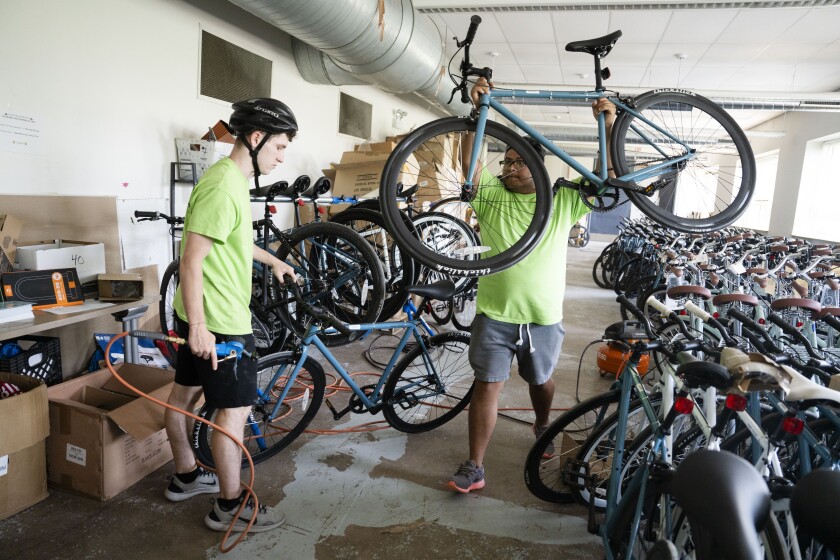
Policy and Certification Impacts
Government policies and certification programs are playing a crucial role in driving the transition to zero-waste manufacturing. Regulations around waste disposal, carbon emissions, and environmental protection are encouraging manufacturers to rethink their operations and invest in sustainable practices.
1. Government Regulations
Across the globe, governments are instituting policies that hold manufacturers accountable for their environmental impact. Policies such as the European Union’s Circular Economy Action Plan, which aims to create a circular economy by reducing waste and promoting recycling, are pushing manufacturers to adopt zero-waste practices. These regulations encourage companies to implement more sustainable production processes, use renewable materials, and minimize energy consumption.
In countries like Japan and South Korea, where recycling and waste management are highly prioritized, strict waste disposal and recycling laws are helping push the manufacturing sector to innovate and minimize waste. Similarly, California’s zero-emission vehicle standards are prompting the automotive industry to adopt cleaner, more sustainable manufacturing processes, including reducing waste during production.
2. Sustainability Certifications
To show their commitment to sustainable practices, many manufacturers are seeking certifications that demonstrate their adherence to strict environmental standards. Certifications such as ISO 14001 (Environmental Management Systems) and Cradle to Cradle certification validate a company’s efforts to minimize waste and create more sustainable products.
Brands that are committed to zero-waste manufacturing can use these certifications as a way to demonstrate their environmental responsibility to consumers, investors, and regulatory bodies. These certifications also help consumers make informed choices by indicating which companies are truly committed to reducing waste and making a positive environmental impact.
Brand Case Studies
Several leading brands are already incorporating zero-waste manufacturing principles into their operations, serving as models for other companies looking to adopt similar practices.
1. Patagonia
Patagonia, the outdoor clothing brand, has long been a pioneer in sustainable business practices. The company uses recycled materials in the production of many of its products, such as recycled polyester and wool, and ensures that its manufacturing processes adhere to strict environmental standards. The company’s “Worn Wear” initiative encourages customers to buy second-hand items, which reduces waste and extends the life of products.
Patagonia’s commitment to sustainability is reflected in its supply chain, where it works closely with suppliers to reduce waste, improve energy efficiency, and minimize the environmental impact of its operations. Patagonia is a clear example of a company that is successfully integrating sustainability into every aspect of its business.
2. Tesla
Tesla, the electric vehicle manufacturer, is another leader in zero-waste practices. The company has invested heavily in renewable energy and sustainable manufacturing techniques, including using recycled aluminum in its cars and reducing waste during the production process. Tesla’s Gigafactory, where it manufactures batteries and electric vehicles, is designed to be a zero-emissions facility, and the company is working to ensure that its entire supply chain follows sustainable practices.
Tesla’s approach to zero-waste manufacturing is not limited to the production of electric vehicles. The company has also implemented waste-reducing techniques in the creation of its solar products, aiming to make its entire business more sustainable from end to end.
Conclusion: Are These Efforts Scalable?
The push for zero-waste manufacturing is gaining significant momentum, and many companies are making impressive strides toward reducing waste and implementing sustainable practices. Innovations in molding, welding, materials, and supply chain management are helping manufacturers reduce waste and maximize resource efficiency. Furthermore, government regulations and sustainability certifications are creating an environment where zero-waste practices can thrive.
However, the scalability of these efforts is still a topic of debate. While large corporations such as Patagonia and Tesla have the resources and infrastructure to implement zero-waste manufacturing on a large scale, small and medium-sized businesses may struggle to adopt these practices due to cost and resource limitations. Additionally, widespread adoption of zero-waste manufacturing requires global collaboration, as industries in different regions must come together to share best practices, innovations, and technologies.
Despite these challenges, the future of zero-waste manufacturing looks promising. With continued investment in process innovations, sustainable materials, and regulatory support, the manufacturing industry is poised to transition to a more sustainable and circular model that minimizes waste and maximizes the use of resources.
Discussion about this post