Introduction: Rethinking the Bicycle’s Green Credentials
Bicycles have long symbolized environmental friendliness, providing a clean alternative to cars and helping reduce traffic congestion and carbon emissions. However, there is a growing realization within the industry and cycling community that a bike’s sustainability does not end with how it’s used—it begins with how it’s made. From the materials used in frames and components to the finishes applied, traditional bicycle production has relied heavily on resource-intensive and pollutive processes. As climate concerns intensify and circular economy principles gain traction, bike manufacturers are being pushed to consider eco-friendly materials that align with sustainability goals. This article explores the latest trends in the adoption of sustainable materials in bicycle manufacturing, as well as the challenges that threaten to slow progress.
Traditional Materials and Their Environmental Impact
The majority of bicycles today are built using materials like aluminum, carbon fiber, steel, and plastic-based composites. While each of these materials offers benefits in strength, weight, and cost, they also come with serious environmental drawbacks. Aluminum production, for instance, is highly energy-intensive and requires bauxite mining, which damages ecosystems. Carbon fiber, despite being prized for its high strength-to-weight ratio, is nearly impossible to recycle and generates significant manufacturing waste. Steel is recyclable but often involves considerable emissions in the smelting process. Plastics and synthetic resins used in components and coatings are largely derived from fossil fuels and contribute to microplastic pollution. These issues highlight the urgent need for a shift toward greener alternatives that reduce ecological damage at every stage of the production lifecycle.
Trend 1: Recycled Metals in Frame Construction
One of the most accessible and impactful sustainable shifts in the bicycle industry is the increased use of recycled metals. Recycled aluminum and steel retain much of their structural integrity and can be used to produce frames, forks, and components without compromising safety or performance. Compared to virgin aluminum, recycled aluminum requires up to 95% less energy to produce, significantly reducing emissions. Brands like Trek and Canyon have started integrating recycled aluminum into their urban and commuter bikes. In addition to lowering the carbon footprint, using recycled metals helps minimize mining and the associated destruction of natural habitats. However, one challenge remains in ensuring the consistency and quality of recycled alloys, as contaminants or irregularities can affect welding and long-term durability.
Trend 2: Bamboo and Natural Fiber Frames
For a completely different approach, some manufacturers are turning to nature’s own building materials—bamboo, flax, and hemp. Bamboo is particularly promising due to its rapid growth, renewability, and impressive tensile strength. It also naturally dampens vibrations, making it ideal for comfortable urban and touring rides. Companies like Booomers and My Boo are not only producing bamboo bikes but also supporting local economies in Ghana by employing artisans and reinvesting in community development. Flax and hemp fibers, often combined with bio-resins, are used to reinforce frames and create lightweight composite structures. These natural fibers are biodegradable and often grown with little to no pesticide use. While bamboo bikes are gaining popularity in niche markets, broader adoption is limited by perceptions of fragility and challenges in quality control, especially in high-performance cycling segments.
Trend 3: Bio-Based Plastics and Resins
Petroleum-based plastics are ubiquitous in modern bike components—from saddles and grips to pedal cages and accessories. To counteract the environmental toll, several companies are exploring bioplastics made from renewable sources such as corn starch, castor beans, and sugarcane. These bio-based polymers have similar performance characteristics but decompose more readily and carry a smaller carbon footprint. In parallel, the use of plant-based resins is growing in composite frame production. These resins can replace traditional epoxies in binding carbon or natural fibers, offering a lower-toxicity alternative. For example, Greenpoxy and Super Sap are bio-resin brands now used in some cycling applications. Despite the environmental benefits, bioplastics and bio-resins remain more expensive than conventional materials and may have slightly lower mechanical performance, presenting trade-offs that manufacturers must weigh.
Trend 4: Recycled Carbon Fiber Applications
Carbon fiber remains a staple in high-performance bicycle manufacturing, but its sustainability challenges are significant. Traditional carbon composites are difficult to recycle due to the cross-linked polymer matrix, and most manufacturing waste ends up in landfills. However, recent advances in carbon fiber reclamation offer hope. Several companies are pioneering processes to chop and repurpose carbon fiber from production scrap or end-of-life products. The resulting short-fiber material can be molded into components like handlebars, seatposts, and even frames for recreational use. While not suitable for elite racing applications, recycled carbon fiber offers sufficient strength for commuting and e-bikes. Scaling these technologies remains a hurdle, particularly as reclaimed carbon must be carefully processed to ensure quality and reliability.
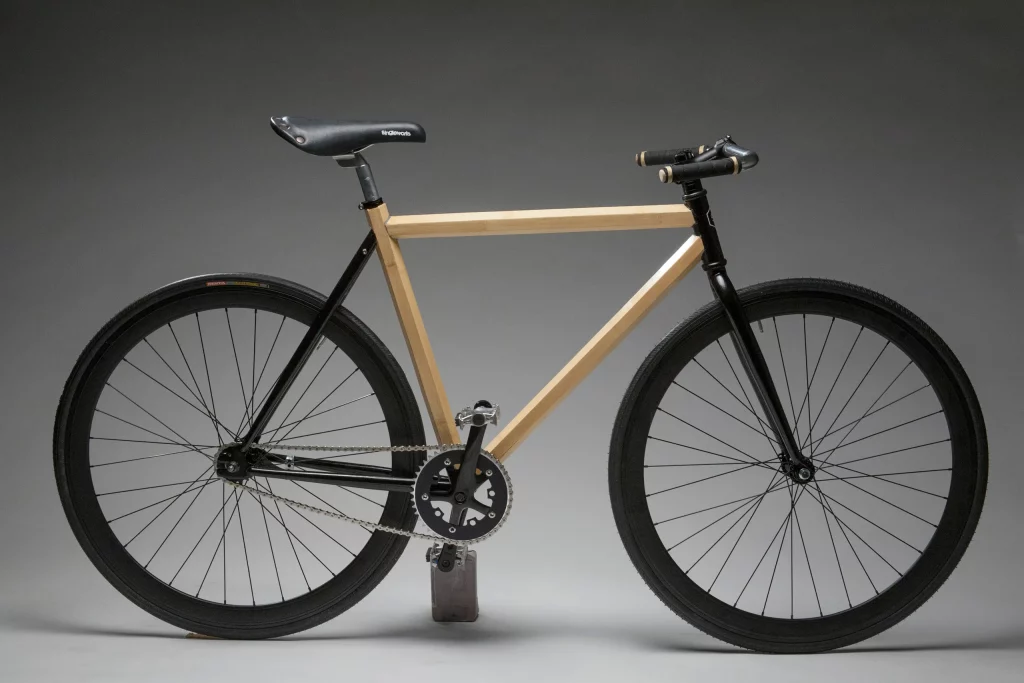
Trend 5: Sustainable Finishing Techniques and Coatings
A less visible but equally impactful area of bicycle sustainability lies in the paints, finishes, and adhesives used throughout production. Many traditional coatings contain volatile organic compounds (VOCs), which contribute to air pollution and pose health risks to workers. In response, some manufacturers are adopting water-based paints, powder coatings, and anodizing processes that eliminate or greatly reduce VOC emissions. Powder coating, in particular, is gaining popularity due to its durability, waste reduction, and solvent-free nature. Anodizing offers a lightweight and corrosion-resistant finish for aluminum frames without the need for paint. These sustainable finishing techniques not only reduce environmental impact but also improve workplace safety and create aesthetically appealing products with minimal ecological cost.
Challenges to Adoption
1. Cost Constraints
One of the main barriers to adopting sustainable materials is the cost. Eco-friendly alternatives—whether recycled metals, bioplastics, or natural fibers—tend to be more expensive due to limited supply chains, specialized processing needs, and economies of scale. For brands operating in competitive markets with thin margins, passing these costs onto consumers can be risky. Government subsidies or certifications could help bridge this gap, but such incentives remain limited in most regions.
2. Performance Trade-Offs
While many eco-friendly materials perform well in everyday cycling scenarios, they may not match the strength-to-weight ratio or longevity of their traditional counterparts in high-performance applications. Professional riders and competitive cyclists often prioritize weight and stiffness, making them hesitant to adopt newer, less-proven materials. Continued R&D is needed to improve the technical specifications of sustainable options without compromising on performance.
3. Limited Infrastructure and Supply Chains
Sourcing sustainable materials requires reliable and scalable infrastructure. Unfortunately, the global supply chain for green materials is still underdeveloped. Suppliers of bio-resins or recycled carbon fiber are relatively few, and access to natural materials like bamboo or flax depends heavily on geographic location. Without consistent availability, manufacturers face bottlenecks and uncertainty in their production timelines.
4. Consumer Awareness and Demand
While sustainability is a growing concern among consumers, many still prioritize price, performance, and brand prestige over environmental impact. Until eco-conscious behavior becomes more mainstream, manufacturers may struggle to justify the investment in greener production methods. Educating consumers about the long-term benefits of sustainable bikes—including lower environmental costs and healthier work environments—is crucial for market growth.
5. Lifecycle and End-of-Life Solutions
Sustainability doesn’t end with material sourcing—it also involves what happens when a bike reaches the end of its life. Currently, most bike frames, especially those made from carbon fiber or complex composites, are not easily recyclable. Developing end-of-life solutions such as take-back programs, remanufacturing, and component recycling is essential for closing the loop. A truly sustainable bike must be designed with its entire lifecycle in mind.
The Road Ahead: Innovation and Collaboration
The transition to eco-friendly materials in bicycle production is not a solitary endeavor. It requires collaboration between manufacturers, material scientists, regulators, and consumers. Encouragingly, innovation in this space is accelerating. University research programs are developing next-generation composites, startups are piloting closed-loop production models, and large brands are beginning to set ambitious sustainability targets. For instance, Decathlon and Shimano have both released sustainability roadmaps with commitments to lower emissions and use more recycled materials by 2030. Such initiatives show that change is possible—but only if sustainability is woven into every layer of the design and production process.
Conclusion: Greening the Ride from Frame to Finish
The bicycle industry stands at a pivotal moment. As environmental concerns mount and consumer expectations evolve, manufacturers are being called upon to move beyond the old model of resource-heavy production and embrace a future defined by sustainability and innovation. Whether through bamboo frames, bio-based plastics, or water-based finishes, each eco-friendly advancement brings us closer to a truly green cycling experience. While challenges remain, the industry’s shift toward sustainable materials is not just a trend—it’s a necessity. By embracing this shift, we not only preserve the planet we ride through but also ensure that future generations can continue to experience the joy, freedom, and health benefits that bicycles provide.
Discussion about this post